Specialist Recommendations on What is Porosity in Welding and Exactly How to Address It
Specialist Recommendations on What is Porosity in Welding and Exactly How to Address It
Blog Article
The Science Behind Porosity: A Comprehensive Overview for Welders and Fabricators
Comprehending the complex devices behind porosity in welding is crucial for welders and fabricators aiming for flawless workmanship. From the make-up of the base materials to the ins and outs of the welding procedure itself, a plethora of variables conspire to either exacerbate or minimize the visibility of porosity.
Comprehending Porosity in Welding
FIRST SENTENCE:
Examination of porosity in welding discloses critical understandings right into the integrity and quality of the weld joint. Porosity, characterized by the presence of cavities or voids within the weld metal, is a common problem in welding procedures. These gaps, otherwise appropriately attended to, can compromise the structural integrity and mechanical homes of the weld, bring about possible failings in the completed product.
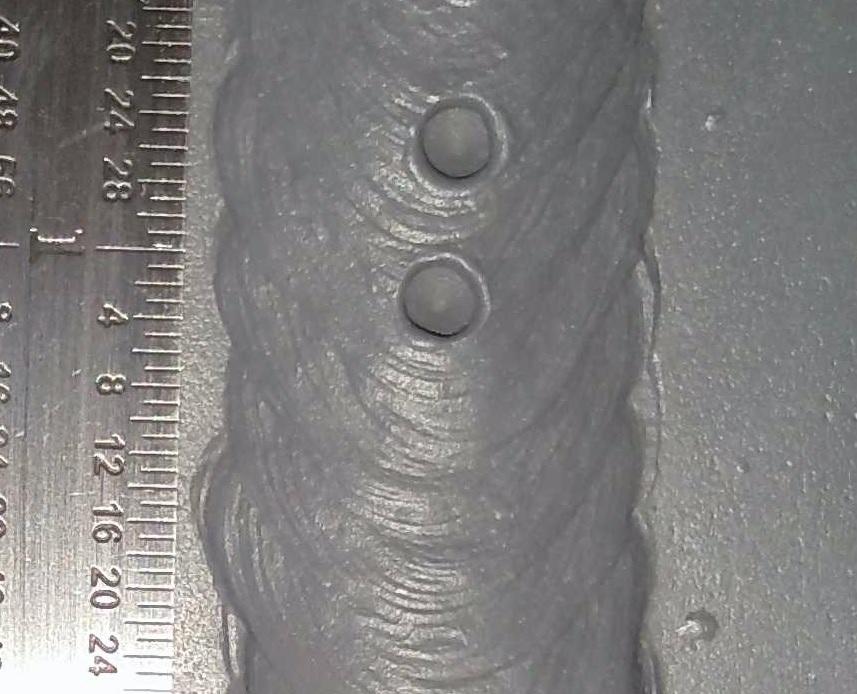
To identify and evaluate porosity, non-destructive testing methods such as ultrasonic screening or X-ray examination are usually utilized. These techniques enable the recognition of interior problems without compromising the honesty of the weld. By examining the size, form, and circulation of porosity within a weld, welders can make educated decisions to boost their welding processes and achieve sounder weld joints.

Aspects Influencing Porosity Formation
The event of porosity in welding is affected by a myriad of aspects, ranging from gas shielding effectiveness to the intricacies of welding criterion setups. One vital element adding to porosity development is inadequate gas securing. When the securing gas, commonly argon or carbon dioxide, is not efficiently covering the weld swimming pool, climatic gases like oxygen and nitrogen can infect the molten steel, bring about porosity. Additionally, the tidiness of the base materials plays a significant function. Contaminants such as corrosion, oil, or wetness can evaporate during welding, creating gas pockets within the weld. Welding criteria, including voltage, existing, travel rate, and electrode kind, also impact porosity development. Utilizing incorrect settings can generate excessive spatter or warm input, which in turn can lead to porosity. Furthermore, the welding strategy utilized, such as gas steel arc welding (GMAW) or secured metal arc welding (SMAW), can affect porosity development due to variants in heat circulation and gas protection. Recognizing and controlling these factors are essential for decreasing porosity in welding operations.
Effects of Porosity on Weld High Quality
The existence of porosity also damages the weld's resistance to rust, as the trapped air or gases within the gaps can react look at this web-site with the surrounding environment, leading to destruction over time. Furthermore, porosity can prevent the weld's capability to endure stress or effect, further threatening the overall top quality and reliability of the bonded structure. In essential applications such as aerospace, vehicle, or structural building and constructions, where safety and longevity are vital, the detrimental effects of porosity on weld high quality can have severe effects, emphasizing the relevance of reducing porosity through appropriate welding strategies and procedures.
Strategies to Minimize Porosity
To boost the quality of welded joints and make certain structural stability, welders and fabricators utilize details techniques focused on lowering the formation of spaces and dental caries within the material during the welding procedure. One effective technique to decrease porosity is to make certain proper material prep work. This consists of comprehensive cleansing of the base steel to remove any pollutants such as oil, oil, or moisture that could add to porosity development. Additionally, utilizing the appropriate welding parameters, such as the right voltage, existing, and take a trip speed, is important in preventing porosity. Preserving a regular arc size and angle during welding also helps in reducing the likelihood of porosity.

Utilizing the suitable welding strategy, such as back-stepping or utilizing a weaving motion, can Recommended Site additionally assist distribute heat equally and lower the opportunities of porosity development. By carrying out these techniques, welders can effectively minimize porosity and generate high-grade bonded joints.

Advanced Solutions for Porosity Control
Carrying out innovative technologies and cutting-edge techniques plays a pivotal duty in achieving exceptional control over porosity in welding processes. anchor Furthermore, employing innovative welding techniques such as pulsed MIG welding or customized environment welding can additionally help alleviate porosity concerns.
An additional advanced remedy involves making use of sophisticated welding devices. For example, using equipment with built-in attributes like waveform control and sophisticated power resources can enhance weld top quality and minimize porosity risks. Furthermore, the application of automated welding systems with specific control over parameters can dramatically reduce porosity flaws.
In addition, incorporating advanced tracking and examination technologies such as real-time X-ray imaging or automated ultrasonic testing can help in identifying porosity early in the welding process, permitting instant restorative activities. On the whole, incorporating these advanced services can considerably enhance porosity control and boost the total top quality of welded components.
Conclusion
In conclusion, recognizing the scientific research behind porosity in welding is necessary for welders and producers to create top quality welds - What is Porosity. Advanced solutions for porosity control can further boost the welding procedure and guarantee a strong and reliable weld.
Report this page